Computer software plays a crucial role in the operation and functioning of a CO2 laser cutting machine in several ways:
- Design Preparation:
- CAD/CAM Software: Computer-Aided Design (CAD) and Computer-Aided Manufacturing (CAM) software help create and prepare designs for cutting. Users can design or import digital drawings, which the software translates into machine-readable instructions.
- File Processing and Conversion:
- Vectorization: The software converts design files into vector formats, such as DXF or AI, containing precise lines, shapes, and paths that the laser cutter can interpret for cutting or engraving.
- File Compatibility: Software ensures compatibility with the machine’s control system, allowing seamless transfer of cutting instructions.
- Job Control and Settings:
- Machine Control: Specialized software controls the laser machine, managing parameters like laser power, speed, focal length, and path of the laser beam. It translates design specifications into commands that the machine executes.
- Job Management: Software often includes job management features, allowing users to organize, schedule, and queue up different cutting or engraving jobs.
- Precision and Accuracy:
- Path Optimization: Software optimizes cutting paths to maximize efficiency, reduce material waste, and ensure accurate cutting or engraving according to the design specifications.
- Resolution Control: It manages the resolution and precision of cuts or engravings, ensuring high-quality output based on the desired level of detail.
- User Interface and Control:
- User-Friendly Interface: The software provides a user-friendly interface for operators to interact with the machine, allowing them to adjust settings, preview designs, and monitor the cutting process.
- Diagnostic and Reporting Tools: Some software includes diagnostic tools and reporting features to monitor machine status, detect errors, and generate reports on job completion or machine performance.
- Safety and Monitoring:
- Safety Protocols: Software may integrate safety protocols to ensure proper operation and adherence to safety guidelines, such as emergency stop functions or interlocks.
- Real-Time Monitoring: It facilitates real-time monitoring of the cutting process, enabling operators to intervene or adjust settings if needed.
The computer software acts as the intermediary between the user’s design intentions and the CO2 laser cutting machine, translating design files into machine-readable instructions and controlling the entire cutting or engraving process, ensuring precision, Co2 Laser cutting machine efficiency, and control over the final output.
How is the laser controlled to achieve precise and accurate Co2 Laser cutting machine?
Achieving precise and accurate cuts with a CO2 laser cutting machine involves precise control of various parameters and components:
- Laser Beam Characteristics:
- Power Control: The laser’s power output determines the intensity of the beam. Precise control over power settings ensures the right amount of energy for different materials and thicknesses.
- Beam Focus: Controlling the focal length ensures the laser beam concentrates at the correct point on the material, affecting the cut’s depth and precision.
- Motion Control:
- X-Y Axis Control: Precise movement of the cutting head along the X and Y axes dictates the path and shape of the cut. Motors and motion control systems guide the laser head accurately according to the design specifications.
- Acceleration and Speed: Controlling the speed and acceleration of the laser head movement ensures accurate cuts at varying speeds without compromising quality.
- Material Parameters:
- Material Settings: Parameters such as the type, thickness, and density of the material being cut are crucial. The software adjusts the laser settings based on these material parameters for optimal cutting results.
- Pulse and Modulation Control:
- Pulse Frequency: Some systems use pulsed laser beams for precise control over the amount of energy delivered to the material. Modulating the pulse frequency can affect the depth and quality of the cut.
- Duty Cycle: Controlling the laser’s duty cycle, the ratio of the laser’s on-time to off-time, regulates the amount of heat applied to the material, impacting the cutting quality.
- Precision Sensors and Feedback Systems:
- Position Sensors: High-precision sensors provide feedback on the laser head’s position, ensuring accuracy in movement and alignment.
- Real-Time Feedback: Systems often incorporate real-time feedback mechanisms to monitor cutting parameters and adjust settings dynamically during the cutting process for optimal results.
- Optics and Beam Delivery:
- Mirrors and Lenses: Precise alignment and cleanliness of mirrors and lenses direct the laser beam accurately, ensuring it maintains its quality and focus throughout the cutting process.
- Calibration and Maintenance:
- Regular Calibration: Routine calibration of the machine’s components ensures accurate and consistent cutting results over time.
- Maintenance: Proper maintenance, including cleaning optics, checking alignment, and replacing worn components, helps maintain precision and accuracy.
By carefully controlling these parameters and systems, CO2 laser cutting machines can achieve highly precise and accurate cuts on a wide range of materials, meeting specific design requirements with minimal errors or deviations.
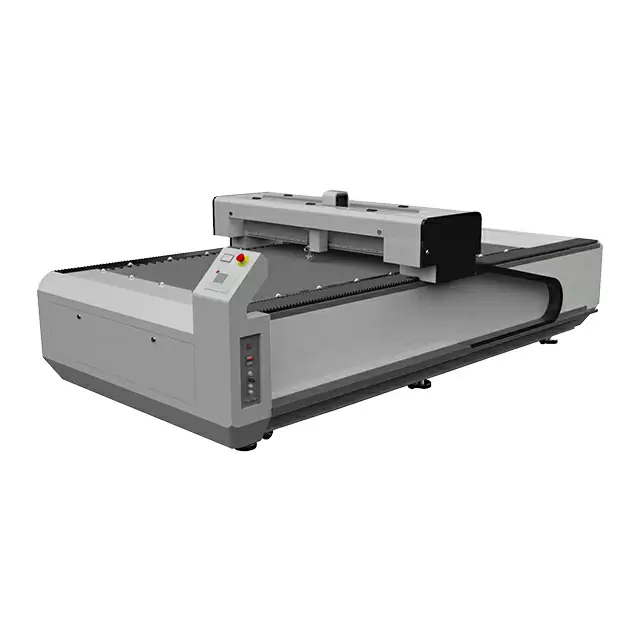
Leave a Reply